The ignition hero that's been firing engines for over a century
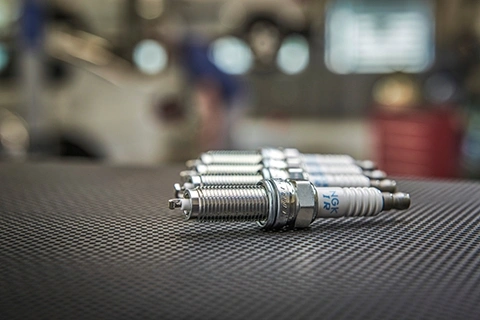
An expertise in ceramics
NGK SPARK PLUG, the world’s leading spark plug manufacturer, has its original roots in a company that manufactured ceramics. The idea to get involved in the production of spark plugs came when Magoemon Ezoe visited the US in 1920. Ezoe, a general manager of this company, had initially planned to observe how the American insulator industry functioned. During his business trip, however, he was also given the opportunity to visit a spark plug factory in Detroit.
Ezoe’s interest in the topic was sparked. He returned to his native Japan convinced that his company’s expertise in ceramics would be an added advantage in the production of spark plugs. He wasn’t wrong. NGK SPARK PLUG was created as a separate entity in the 1930s. Through a commitment to innovation that’s been evident ever since, the company has contributed extensively to the development of this integral ignition device.
The enduring design principle
The mighty spark plug has been a hero of ignition ever since its introduction in the early 20th century, igniting the air-fuel mixture in engines that creates combustion which pushes the pistons down. Before its invention, systems such as naked flames and glow tubes were used in the ignition process. These systems, however, were unreliable and presented what Carl Benz referred to as a ‘fundamental obstacle’ to early motoring.
The spark plug easily overcame this hurdle. Such has been its success, that the original design principle that was used by NGK SPARK PLUG in the 1930s has not been altered. “Just like the four-stroke engine, the basic principle of how a spark plug functions hasn’t changed since they first started being used in automobiles”, says Kai Wilschrei, Senior Manager Technical Services Aftermarket EMEA at NGK SPARK PLUG EUROPE. “A spark plug is still screwed in, consisting basically of a thread, a metal sleeve, electrodes and a ceramic insulator.”
Automobile innovation through the decades, however, has been rapid; having a knock-on effect on how spark plugs are created. “The spark plugs we make today must be able to withstand much higher voltages, pressures and temperatures, as well as dissipating more heat”, he says.
Innovation is key
To improve spark plug efficiency, the company started to manufacture ‘copper-core wide range’ spark plugs in 1965, which became a pioneer product in the automobile industry. “The addition of a copper core in the ground electrode provided superior heat dissipation to the spark plug because copper is a better heat conductor than metal”, explains Wilschrei.
A further major innovation in spark plug technology was the introduction of ‘V-groove’ in 1979. Named because of its v-shaped centre electrode, the V-groove’s design forced the spark to occur at the outer edge of the electrode, making the air-fuel mixture easier to ignite, while also reducing the voltage required to produce a spark. Due to its improved ignitability, V-groove continues to be a popular Aftermarket choice.
Precious metals: a giant leap in spark plug development
The introduction of precious metals Platinum (1982) and Iridium (1996) into its product range was a giant leap for NGK SPARK PLUG. The company’s range of precious metal spark plugs “provide higher ignitability and longer service life over conventional spark plugs. This is because of their higher melting points over traditional metals such as nickel”, says Wilschrei.
Much higher melting points allow the centre electrode diameters to reduce from 2.5mm using Nickel, to 0.6mm using Iridium or Platinum. “A more complete burn is possible because of this, which translates into improved acceleration and fuel consumption as well as smoother idling”, explains the expert.
Today, the company builds two types of iridium spark plugs: ‘Laser Iridium’, which is available in OE vehicles and as a direct replacement on the Aftermarket and ‘Iridium IX’, an Aftermarket upgrade for engines that were originally equipped with standard nickel spark plugs. “In 2009, we also launched ‘LPG LaserLine’, a state-of-the-art precious metal spark plug; the very first one specifically designed for gas engines”, says Wilschrei.
Racing: the toughest test arena
Precious metal spark plugs are also used in the world of motorsport, where the company has a long and illustrious history. Partnerships with teams in all varieties of motorsport such as Formula 1, WRC, MotoGP, WSBK and MXGP have allowed the company to prove their spark plugs in the most extreme of conditions. “Laboratory and road testing alone aren’t enough. To continually deliver enhanced engine parts that excel in the most demanding driving conditions, you have to prove them at the top level of motorsport because it provides the toughest test possible”, says Wilschrei.
The company’s participation in motor racing, which in some cases has resulted in the development of tailor-made racing components for specific teams, has had a domino-like impact outside of the fast lane. “We apply our motorsport knowledge to our OE and Aftermarket products, in order to benefit customers and everyday drivers. Our precious metal spark plugs, for example, began in F1 but are now common OE in passenger cars, bringing driving and environmental benefits to us all”, reveals the expert.
According to Wilschrei, examples such as the company’s involvement in motor racing or its creation of a spark plug range for a niche fuel like gas, perfectly encapsulate the company’s values. “No matter the engine, we are dedicated to manufacturing a spark plug that is the perfect match. That is why we produce more than 1500 different kinds of spark plugs”, he says.