Tips and tricks on avoiding the most common ignition problems
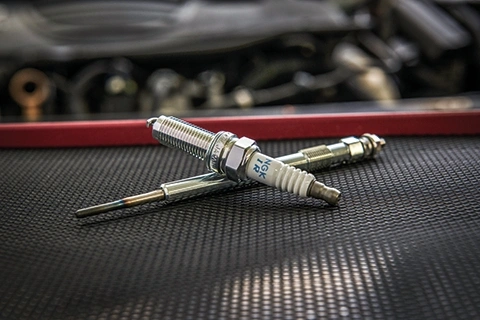
How to avoid carbon fouling in spark plugs
This is by far the most common type of spark plug problem. Unfortunately, such warranty claims are rejected because carbon fouling occurs due external factors, not manufacturing errors. When a spark plug is fouled, the insulator nose at the firing tip is coated with a foreign substance such as fuel, oil, or carbon, resulting in the engine misfiring or failing to start. “Instead of bridging the electrode gap and firing normally like it is supposed to, this coating makes it easier for the voltage to follow along the insulator nose, leak back down into the metal shell and ground out,” says Kai Wilschrei, Senior Manager Technical Service Aftermarket EMEA at NGK SPARK PLUG EUROPE.
“Common reasons for this include the wrong spark plug heat range, a non-optimal engine combustion process and poor running conditions like continuous low-speed driving and short trips,” explains the expert. “For example, a spark plug must reach a temperature of 450°C before it starts to self-clean by burning off carbon deposits. Regular short trips and continuous low-speed driving, however, result in the spark plug being unable to reach this critical temperature, making conditions for fouling ripe,” he warns.
Luckily, there are many precautions that can be taken to prevent this from occurring. The expert recommends, “making sure that the engine’s air/fuel mixture is correct, regularly checking ignition system components such as wires, coils and caps for signs of wear and tear, driving at faster speeds for longer periods of time every now and then and using a spark plug that has the correct heat range.”
Interestingly, he reveals, some of the fouled spark plugs which have been sent back as warranty claims actually function perfectly once they have been cleaned. “This demonstrates the vital role the aforementioned external factors can play on both spark plugs and overall engine health. Simply replacing a fouled spark plug with a new one may solve the problem temporarily but in truth, it just postpones it till a later date,” he says.
The correct torque is vital
Another common cause of rejected warranty claims is due to the incorrect tightening torque during installation. If the torque is set too low, there is a risk of compression loss and overheating of the spark plug. Additionally, the insulator and electrodes may also be damaged as a result of excessive vibrations.
On the other hand, if the torque is set too high, the metal shell of the spark plug will be over-stressed, increasing the likelihood of it yielding or expanding. Expansion can cause the heat dissipation zones to be disrupted. Overheating, melting of the electrodes and even engine damage are other potential outcomes.
“It is essential to tighten a spark plug to the specified turning angle or torque setting,” says Mr. Wilschrei. “First, clean the spark plug holes of lubricant, dirt and debris. Then screw in the plug finger tight until the gasket meets the cylinder head. ‘Seat’ the plug/gasket with a torque wrench to the specified torque. If you use a standard wrench, turn it to the indicated angle,” he says.
The use of a spark plug socket suitable for the installation is another important factor that is often overlooked. “Such a socket should ensure that the spark plug can fit securely into it,” explains Mr. Wilschrei. “The use of a poor-quality socket can crack the ceramic insulator during installation, leading the engine to misfire,” he informs.
Important to remember also is that in certain vehicles, the use of non-standard tools is necessary for correct spark plug installation. “Our warranty department receives a growing number of ZKBR7A-HTU spark plugs with the warranty claim that they had failed or were misfiring. All these spark plugs were installed either in BMW N43 (4 Cylinder) or N53 (6 Cylinder) engines,” informs the expert. “In these particular engines, however, the spark plugs are installed at an angle of more than 5°. The installation of spark plugs in these particular engines can only be done with a special socket featuring an articulated joint. The testing we carried out on the returned plugs found that this mandatory tool had not been used, meaning we unfortunately had to reject the warranty claims,” he says.
Glow plug removal and installation
Excessive heat due to fuel leaking from the injectors, too much voltage caused by a faulty controller or dirt in the glow plug hole, are some of the most common reasons for a glow plug to malfunction in diesel engines. This will require its replacement which also has the potential to cause problems. According to Mr. Wilschrei, however, any issues can easily be avoided if one adheres to the correct precautionary steps. “When a glow plug needs to be replaced, it is recommended to apply a synthetic engine oil around each glow plug and ideally let it penetrate for at least a week. This reduces the risk of shearing and makes removal easier,” he says.
“When starting to remove the glow plugs, warm up the engine since glow plugs loosen more easily when the engine is hot, and use a suitable torque wrench capable of measuring loosening torque, set to the shear values. Once the glow plug is removed, use a glow plug hole reamer loaded with silicone-free grease to clean and empty each hole of carbon deposits. Finally, manually install the new glow plugs into their seats and tighten using a correctly set torque wrench,” he recommends.
The benefits of warranty claim testing
Although the testing carried out on warranty claims plays an important role in terms of detecting the source of the failure, for Mr. Wilschrei, it provides additional benefits. “It naturally allows us to improve the quality of our products, but it also helps us to educate our customers about how to save money by keeping their cars’ ignition systems healthy,” he says.
“For anybody who wishes to learn more, I would highly recommend visiting TekniWiki (www.tekniwiki.com), the technical information platform of NGK SPARK PLUG. This interactive hub provides detailed and easy to understand information regarding maintenance, removal and installation of all our company’s products,” he emphasises.