Global presence: The worldwide footprint that is the source of NGK SPARK PLUG's growth, and its foundation for success in a changing future
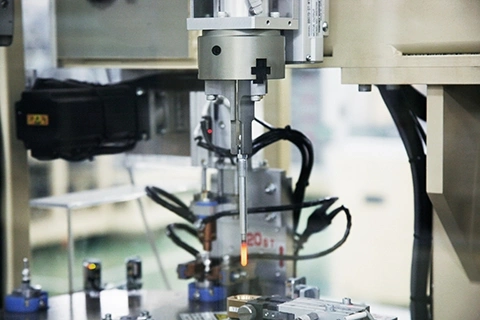
As Damien Germès, Regional President EMEA, President & CEO NGK SPARK PLUG EUROPE and Corporate Officer confirms: “Our production network offers value creation to the world. Not only are we working towards expanding our market share, we are also contributing to a sustainable society by developing products related to the environment, energy, next generation vehicles and the medical field. By combining our manufacturing strengths with the right mindset, we can embrace the challenges of the new era.”
The scale and scope of NGK SPARK PLUG’s activities are impressive. It employs almost 16,000 people across 41 subsidiaries, four Technical Centres and numerous sales offices across 21 countries worldwide. But its key capital asset is a continually growing network of 29 production sites, with an impressive annual capacity of around 1 billion spark plugs sold to over 160 countries.
From that foundation the company has become a world-leading ignition parts and sensors specialist for 4-wheel, 2-wheel, industry, marine, gardening, agriculture and other internal combustion engines, which it supplies to both the Original Equipment (OE) and the Independent Aftermarket (IAM) sectors. Managed by its Automotive Components business unit, these markets generated 80% of NGK SPARK PLUG’s net sales in fiscal year 2018. The company also excels in state-of-the-art ceramics technologies for life-enhancing applications such as computers, optical communication, wireless networks, medical equipment, space and aeronautics.
Global yet local
The extensive infrastructure that NGK SPARK PLUG created to supply these highly specialised products combines global capability with localised knowledge and flexibility; putting it in a unique position. Organised into five key regions – EMEA (Europe, Middle East and South Africa), South America, North America & Australia, Asia and Japan where the global headquarters is situated – the plants and their associated sales offices are located close to major Original Equipment customers. Including the generation of many raw materials, the majority of its OE and Aftermarket parts are manufactured in-house. Multiple types of the highest volume seller, spark plugs, are made at most sites to guarantee optimum geographic availability. Certain specialised items such as insulator parts however are mostly produced by the company in Japan and assembled locally.
“Our international, yet regional manufacturing and sales network means we can produce consistently high quality and respond to our customers’ fast-developing expectations anywhere worldwide,” continues Damien Germès. “These are also the same qualities that will help us succeed into the future. As new powertrains, globalisation, digitisation, competition and environmental regulations reshape the mobility and technical ceramic industries, our organisation is in the best possible position to evolve and harness new opportunities.”
From Japan to the world
The company’s journey to expansion began in Nagoya, Japan. In 1919, businessman Magoemon Ezoe had resolved to “manufacture spark plugs using ceramics, a speciality of our country Japan”, and NGK INSULATORS was born. The spin-off of its Spark Plug Division in 1936 created NGK SPARK PLUG. By the late 1950s Japan’s economy was rapidly expanding – and as its exports increased, NGK SPARK PLUG took the opportunity to open its first overseas base in Brazil. Its European subsidiary, now called NGK SPARK PLUG EUROPE, opened in 1979; and last year its sales in the EMEA region accounted for 26.1% of the global turnover. Of its seven plants, those in the Americas produce both plugs and sensors, whilst those in Europe and South Africa focus on spark plugs. Developing regions are also under the company’s microscope. “We are getting our production and sales network up to full speed in Brazil, Russia, India and China as well as other emerging markets,” says Germès.
Crucially however, the main emphasis is now on optimising existing assets. “Our financial results have continued to excel, but we must manage the business shrewdly and be responsive to future market evolution,” the Regional President affirms. “We have therefore focused on increasing our capabilities at each site rather than opening new ones. For example, we are expanding our spark plug capacity in Thailand. The Komaki plant is being rebuilt, and we plan to enhance automation at the factory. It’s an ongoing investment and improvement policy.”
Adding value
The success of each NGK SPARK PLUG factory naturally relies on the wider framework of innovation, logistics, quality assurance and even disaster recovery preparation in place, all of which receive significant investment.
Manufacturing techniques are at the very highest levels across the company, with robotisation playing a part. “Our systems are continually evolving. We already use automatic transfer robots and image inspection where appropriate. We may also incorporate artificial intelligence (AI) and the Internet of Things (IoT) to increase connectivity between our machines and make advanced use of the data they generate,” he reveals.
In terms of quality management, all of NGK SPARK PLUG plants are certified to ISO 9001:2015, and most have also achieved ISO TS 16949 and the Industry Automotive Task Force standard, IATF16949. The concept of quality is also driven by employees, thanks to a shared corporate philosophy known as the ‘Nittoku Way’. Germès explains: “Part of this, ‘Shisei-Shinjitsu, means ‘Sincerely, do our very best’. This inspires our teams in every factory, every day.”
The company’s environmental approach is equally fundamental to its many sites. As well as being certified to ISO 14001:2015, verifying its exceptional environmental responsibility, the company has a group-wide policy to ensure systematic, effective environmental conservation. Under ‘Global Eco Vision 2020’, established in 2016, the responsible management of ‘natural resources’, ‘global warming’, ‘toxic, hazardous chemicals’ and ‘key quality (environmentally friendly products)’ are all proactively tackled through wide-ranging special initiatives.
The personal touch
The size and scope of NGK SPARK PLUG’s production footprint brings another important advantage: knowledge. By sharing best practice templates across international borders, the whole organisation is able to stay ahead of the field.
NGK SPARK PLUG factories also reach outside the company in a number of ways. Car makers and distributors regularly visit its locations to see manufacturing in action, and when new products and lines are launched. As a major employer, each site also works in close collaboration with its local community. “More than 1,000 residents took part in plant tours last year to gain an insight into what we do,” adds Damien Germès. “We see such initiatives as a key way to improve communications and understanding with our communities, as well as gathering feedback and goodwill along the way.”
Looking ahead, NGK SPARK PLUG is already evolving its global production infrastructure to optimise additional aspects of mobility or even completely new fields. “Our choices will be determined by business intelligence, technologies and wider economic, environmental and market factors,” Germès concludes. “We can look forward to exciting, challenging times ahead, making our company fit for the future.”
Factory firsts
Japan remains NGK SPARK PLUG’s manufacturing heartland, home to its headquarters and four of its largest production plants.
- Its global headquarters in Nagoya, the capital of Aichi Prefecture in Japan, sits alongside a large spark plug factory – the company’s first – on the same site
- Nearby, the Komaki plant – which manufactures automotive plugs, sensors, semiconductor components, fine ceramics and medical products – is the company’s largest individual plant in terms of footprint as well as its biggest single employment location, with almost 4,000 people
- Japan is also home to the ignition specialist’s highest volume spark plug plant worldwide, the Kyushu island-based Miyanojo factory, which produces hundreds of millions of spark plugs each year.
Insulator insight
Compact, downsized automotive engines have become increasingly common in the fight to improve fuel economy and reduce emissions. To suit this reduced space, spark plugs must now be thinner and longer. They also have to produce the highest ignition performance in an increasingly tough operating environment.
Creating the ultra-thin ceramic insulator sections that are required for spark plugs in these conditions is just one of the precision technologies that NGK SPARK PLUG’s factories produce each day.
Uniform quality
It was NGK SPARK PLUG’s first President, Magoemon Ezoe, who first established the company’s uncompromising attitude to quality that today is continued by every employee. “Suppose we produce only one defective product per 1,000 products,” he said. “To the customer who purchases that one product, our defect rate is 100%.”
More details about NGK SPARK PLUG’s manufacturing sites, activities and ethos can be found at www.ngkntk.com and www.ngkntk.co.jp.